Projects on Decarbonisation and Adaptation to Climate-Related Risks
Estimates show that permafrost areas in Russia total around 11 million km2 (almost two thirds of the country’s total area). It is Eastern Siberia that accounts for most of the permafrost areas.
Permafrost map
Source: National Archives Catalogue, adapted map
Nornickel has been historically operating in permafrost areas. Assets and facilities of its Norilsk and Energy Divisions are located in extremely different permafrost environments. The thickness of permafrost varies from 5 to 200 m and more, and in intermontane valleys, large areas (up to 40%) have taliks even in northern parts of the region. The average annual temperature of rocks varies in a wide range from –5 °С to +5 °С. Discontinuous and sporadic permafrost with a thickness of up to 25 m dominates the Murmansk Region and Zabaykalsky Territory, which are home to the assets of our Kola and Trans-Baikal Divisions.
The current state of permafrost soils is to a large extent shaped by global climate change in the Arctic. Global warming inevitably causes quantitative and qualitative changes in cryolithozone. Combined, the higher average air temperature and man-made impacts on permafrost soils result in a cumulative effect that may undermine the stability of permafrost soils around bases and in natural and engineering disasters. To address this issue and mitigate the accident risk, in 2021 the Company’s Polar Division developed and commissioned an innovative system to monitor the condition of bases and foundations of buildings and structures located in permafrost areas. The project is run in the Norilsk Industrial District across the Company's assets and urban infrastructure facilities and relies on cutting edge automated surveillance solutions and a dedicated software – an information and diagnostics system of the Polar Division.
The project is focused on using automatic equipment to keep real-time track of temperatures in permafrost soils around bases, behaviour in foundations, as well as temperature and humidity levels in crawl spaces. It seeks to help prevent accidents at Nornickel’s industrial facilities and, later on, local housing infrastructure and proactively identify any hazardous defects or deviations that might result in damage to the buildings and structures or their elements, with special safety criteria developed for all monitored indicators. If any such indicator exceeds its threshold, a signal is sent that the facility needs inspection and fixing.
The project's key objectives include:
- design and survey work to obtain more details on the soils around bases, as well as drilling of temperature sensor wells;
- comprehensive inspection of buildings and structures covered by the system;
- introduction of automated monitoring of soils around bases and foundation behaviour to enable faster decision-making and minimise manual measurements;
- creation and implementation of an information and diagnostics system to perform ongoing monitoring of parameters and analyse new data;
- timely repairs of foundations of buildings and structures based on any deviations in monitored metrics to make sure the Company’s infrastructure remains in good working order;
- potential expansion of the list of metrics to be monitored.
The monitoring system relies on:
- thermistor strings to monitor soil temperature within wells;
- piezometer sensors to determine groundwater levels;
- hydrostatic levelling systems and inclinometers for determining deformations of structural elements of buildings;
- strain gauges to measure stress in steel structural elements made;
- thermo hygrometers for operational control of temperature and humidity levels in crawl spaces, including for rapid response to accidents affecting heat and water supply systems;
- satellite monitoring systems to identify movements of structural elements based on decoding and interpretation of multipass spaceborne radar monitoring data.
In 2021, Nornickel upgraded Polar Division’s Buildings and Structures Monitoring Centre, which is responsible for geotechnical monitoring and inspection of facilities. As part of the project, more than 1,200 sensors were installed at 165 facilities. On top of that, 417 new wells were drilled to install temperature sensors inside, thermo hygrometers were set up to control temperature and humidity levels in crawl spaces in real time, and geodetic measurements were carried out to determine deformations of structural elements of buildings and structures. In 2021, we also completed a pilot project to start monitoring the condition of 11 backup diesel fuel tanks of NTEC’s HPP-1, HPP-2 and HPP-3.
During 2022, an information and diagnostic system was established and put into operation, and comprehensive inspections were conducted at 154 facilities, each with geotechnical monitoring programmes and safety criteria developed by specialist contractors. For effective data transmission and processing, a control room was deployed and a transparent business process for supervision, monitoring and inspection of buildings and structures was built, including the development of a geotechnical monitoring standard.
“Six months after the system was put on stream, we have decommissioned 15 buildings, with nine of them undergoing capital repairs and six dismantled altogether. Our automated geotechnical monitoring system has helped to make oversight over buildings and structures some 200% more effective without engaging more personnel. At Nornickel, we have also changed our approaches to construction. The monitoring system is now implemented as early as the construction stage. As a result, we can install rebar sensors directly inside building structures.”
Deputy Chief Engineer of Nornickel’s Polar Division
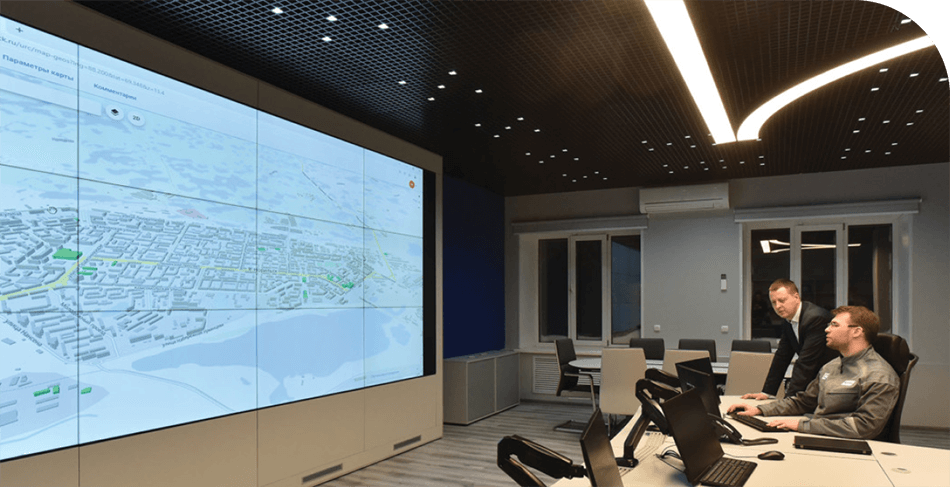
In the medium term, the Company plans to start providing ongoing monitoring data to the academic community for research purposes, including to Fedorovsky Polar State University, which established the Research Centre for Construction Technologies and Monitoring of Buildings and Structures in the Northern Arctic responsible for studying permafrost soils in the Norilsk Industrial District. Other partners are Lomonosov Moscow State University and Bauman Moscow State Technical University, some of Russia’s leading higher education institutions. The Company’s experts are working with researchers to find the best way to develop frost-resistant sensors that will be able to operate at temperatures down to -50–60 °C.
The project’s second stage is fully underway and is scheduled for completion in mid-2024. By that time, monitoring stations are to be put in place at 55 hazardous production facilities of NTEC and four tailing dumps of Norilsk Division’s facilities. Going forward, around 1,500 facilities are planned to be connected to the global information and diagnostics monitoring system, including pump houses and substations, as well as linear facilities: pipelines used for various purposes, pressure hydrotransport, railway tracks, bridge crossings and, possibly, gas pipelines. There are also plans to monitor new facilities under construction.
Nornickel’s project to develop and implement an information and diagnostics system for geotechnical monitoring has won the Project of the Year annual award of the Global CIO expert community as the Best IT Project of the Urals, Siberian, and Far Eastern Federal Districts.
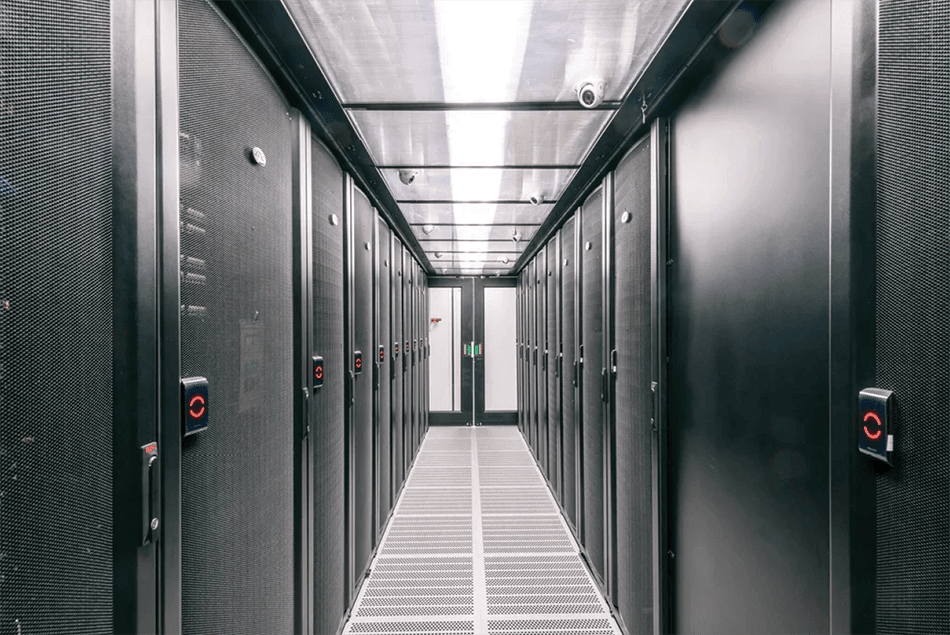
As Norilsk Nickel Group’s key production facilities operate in the harsh climate of the Far North, the Company's fuel and energy services are tasked with a critical mission of ensuring reliable and continuous power supplies.
-
51% of electricity consumed came from renewable sources
More than half of the electricity is generated by two hydropower plants with a total capacity of 1,111 MW:
- Ust-Khantayskaya HPP – 511 MW;
- Kureyskaya HPP – 600 MW.
-
49% of electricity came from gas-fired generation facilities, which have lower GHG emissions as compared to other traditional energy sources
Three combined heat and power plants with a total capacity of 1,115 MW:
- CHPP-1 – 325 MW;
- CHPP-2 – 350 MW;
- CHPP-3 – 440 MW.
-
In addition to CHPPs, there are seven gas boilers that meet Nornickel’s heat needs
One boiler in each of Talnakh, Kayerkan and Alykel, and four boilers in Dudinka provide the district with heat
Below are the Company's key projects and activities aimed at improving the reliability of equipment and reducing physical climate-related risks as well as enhancing energy efficiency and increasing the share of renewables in the energy mix:
Reduction in GHG emissions
Branches and entities of the Company’s divisions annually develop and implement initiatives to save fuel, energy, and water and to ultimately deliver reductions in GHG emissions.
Fuel and energy savings resulting from energy consumption reduction and energy efficiency improvement initiatives in 2022 (TJ)
In 2022, the implementation of operational and technical measures to reduce energy consumption and improve energy efficiency resulted in savings of 362.7 TJ, with efficiency costs totalling RUB 2.2 bn. The savings were achieved due to the measures to switch to LED lighting, improving thermal insulation through the use of modern materials for piping, window and door openings, the use of automatic heat control systems based on changes in ambient temperature, and by introducing automated energy accounting systems for plant workshops.
Renewable energy sources
Nornickel takes a comprehensive approach to energy infrastructure development, combining the objectives of improving the reliability of production assets with those of reducing GHG emissions. We make continuous efforts to reduce the consumption of such energy sources as diesel fuel and coal, and develop alternative energy like hydropower. To that end, Nornickel works consistently to provide its operations with more economical and green energy sources, including in the long term.
The use of renewable energy, such as solar, geothermal and wind energy, is limited by climatic conditions, the length of the polar night and a number of other natural features of the regions where the Company operates. Nevertheless, Nornickel keeps working to find alternative solutions to improve its energy efficiency. In 2022, the Company conducted an analysis of opportunities to switch to green energy sources to replace its own conventional gas power generation facilities in the Norilsk Industrial District in the long term until 2050.
The analysis, carried out for the Norilsk region, revealed that most of the technologies considered as potential options for achieving zero carbon emissions from the Norilsk District's own power generation facilities in the long term to 2050 cannot be implemented under current conditions. Natural and climatic constraints of the Arctic Zone, the requirements of an isolated power system, and the Arctic design of equipment significantly limit the use of direct GHG emission reduction technologies in the Norilsk Industrial District.
Currently, Nornickel cooperates with Rosatom in exploring the possibility of using ground or water-based small modular reactors.
Key energy consumption metrics
Total energy consumption by Norilsk Nickel Group (TJ)
Fuel consumption by Group companies by type of fuel (TJ)
In 2022, total fuel consumption by Group companies decreased by 6.2% compared to 2021 due to lower gasoline and jet fuel costs because of the sale of NordStar Airlines outside the Group's perimeter in 2022. A 3% increase in electricity consumption by 2021 was due to an increase in the consumption by the key operations in the Norilsk Industrial District. Due to higher monthly average temperatures in 2022, there was a 6% reduction in total heat and steam consumption compared to 2021.
Electric power and heat consumption by Group companies (TJ)
Mineralisation of mining waste
In the process of mining, rock is extracted from under the ground and goes to concentrators, where grinding takes place and valuable content is separated from waste rock, or tailings. After that, tailings undergo special treatment and are sent to tailing dumps to be distributed across their surface. During weathering, which is long-term exposure to air, minerals contained in Nornickel’s ores react with carbon dioxide to form secondary carbonates. Combined, Nornickel’s processes of ore mining and delivery to the surface create conditions for carbon dioxide capturing, or mineralisation.
In 2022, Nornickel’s Technology Innovation Department started assessing the potential of carbon dioxide absorption by waste rock removed from the Company's deposits. To study natural mineralisation processes, experts collected around 200 samples of waste rock and sent it to a dedicated research institute to analyse the mineral and chemical composition and therefore to estimate the carbon dioxide absorption potential.
Also, through computer modelling, Nornickel’s experts select optimal process parameters to maximise carbon dioxide absorption. This innovative approach will enable us to manage the mineralisation process and speed it up.
Together with scientists, Nornickel is also developing an engineered mineralisation technology, including by having flue or process gases bubbled through the process slurry at concentrators. Technology of this kind can result in considerably higher volumes of carbon dioxide absorption during production processes.
“We are studying natural mineralisation in order to calculate total GHG volumes absorbed by waste rock at tailing dumps, and to develop a methodology to reflect these in the carbon footprint of our products. The study will enable us to assess the absorbing capacity of tailings based on the mineral composition per tonne of ore mined and process parameters at concentrators.”
Head of Technologies for Recycling and Utilisation of By-Products, Technology Innovation Department
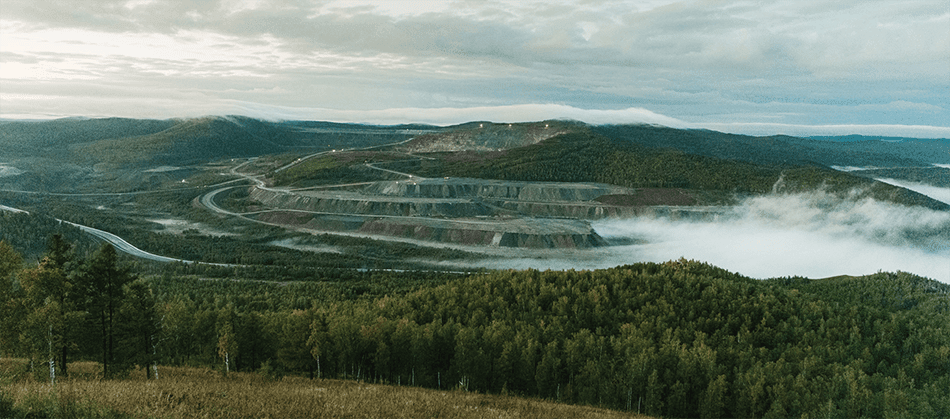
Climate projects
Nornickel is considering potential climate projects to reduce the impact of its operations on climate change. The Company has entered into an agreement with the Siberian Federal University to develop
The Company is putting together a systemic approach to developing climate-related competences by integrating respective aspects into its corporate competence model, which can be used to identify material areas of knowledge for employees of different levels. In the short term, Nornickel plans to introduce a system for assessing competences in the field of climate change and assess knowledge on a regular basis.
The Company also holds seminars on various climate-related matters, engaging leading experts and research organisations. In 2022, more than 200 Nornickel employees took part in the seminars. The Company is also developing a training course for employees on all aspects of the ESG agenda, including climate change.
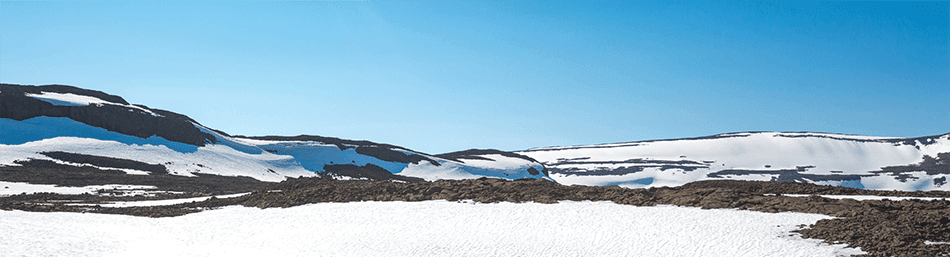